Charging Up the Automotive Industry
The battery market for electric vehicles is going from strength to strength. But it is still characterized by a high level of uncertainty with significant swings in demand. LG Chem is managing this volatility at its giant plant in Poland.
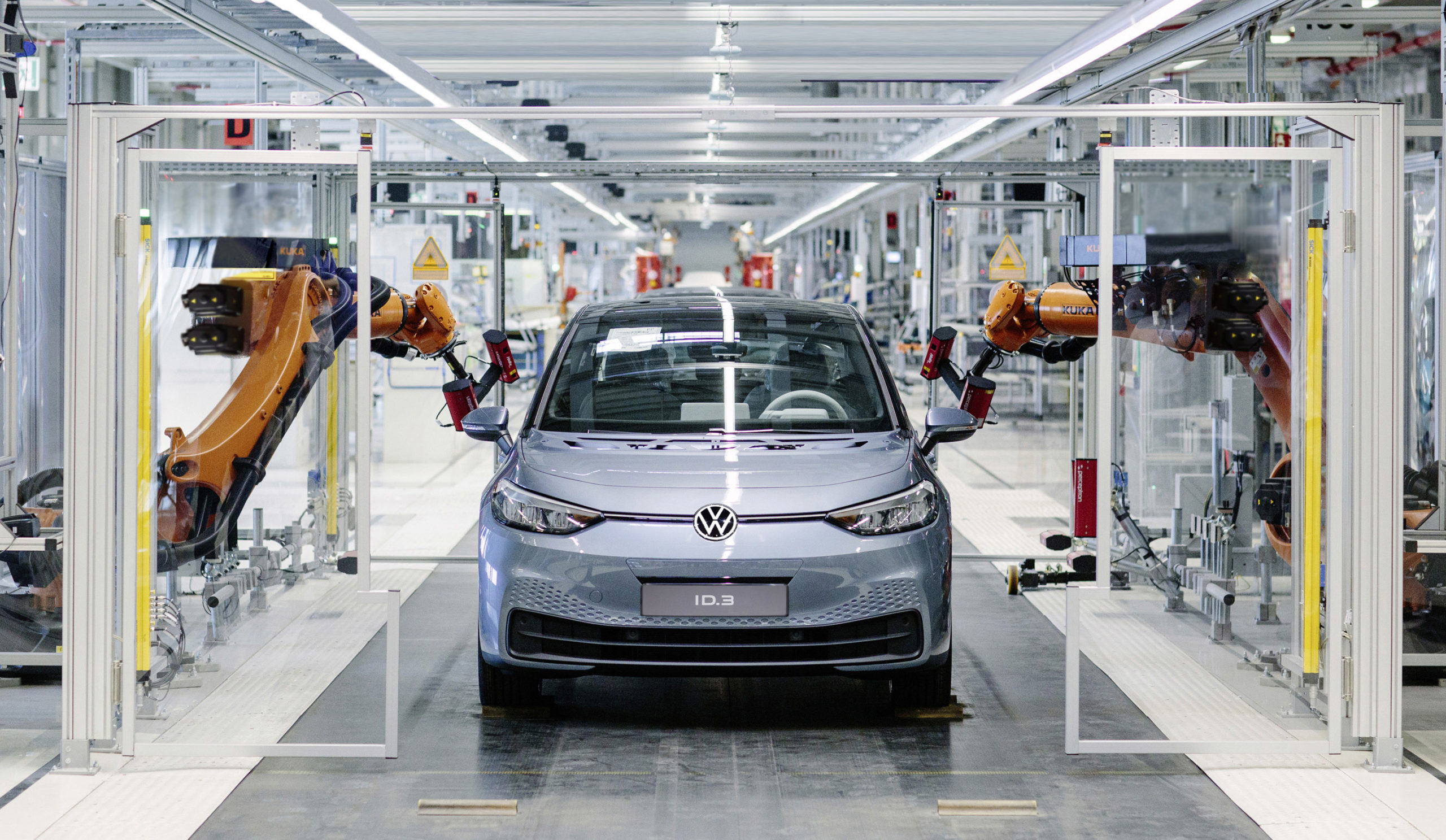
The electrification of the car industry is pushing demand for batteries steadily upwards, with the number of electric and hybrid vehicles anticipated to reach over 90 percent of market share by 2050—up from less than 10 percent in 2018—while the annual production of cars worldwide is expected to double by then. To meet this demand, the production capacity for batteries is predicted to see a seventeen-fold increase measured in gigawatt hours within the same time frame.
LG Chem, number four in the world’s most valuable chemical companies, has over twenty years of experience in the battery market. In 2018, the company built Europe’s largest plant for lithium-ion batteries for electric vehicles. The factory near Wrocław in Poland is four times larger than Tesla’s Gigafactory 1 in the United States. More than fifty production lines supply European car manufacturers with individual cells and complete modules. While the growth forecasts are favorable, LG Chem needs to adapt constantly to very dynamic market conditions. To maintain unprecedented demand and growth, optimization of processes and alignment with OEMs are key.
LG Group
Managing complexity is key
The processes involved are complex, both in terms of manufacturing and in terms of aligning suppliers with OEMs. The production of a pouch cell illustrates this. The lightweight cells go through fifteen production stages with more than 1,500 defined process parameters before they leave the plant after stringent quality controls. Customers like Volkswagen have very specific requirements for their different brands, including technical releases for new products and strict purchase guidelines that suppliers have to adhere to.
For LG Chem, the setup of the plant in Poland was therefore new territory. In order to ensure a smooth launch and to streamline processes, LG Chem commissioned Porsche Consulting to accompany the business through the setup phase. After in-depth assessments, it became apparent that improving equipment maintenance would allow the plant to increase output to meet demand without deploying additional resources. “With the maintenance approach of Porsche Consulting, we can increase our output by 14 percent,” says Kyong Deuk Jeong, President of LG Chem Wrocław Energy.
Passenger car market worldwide
Electrification on the rise
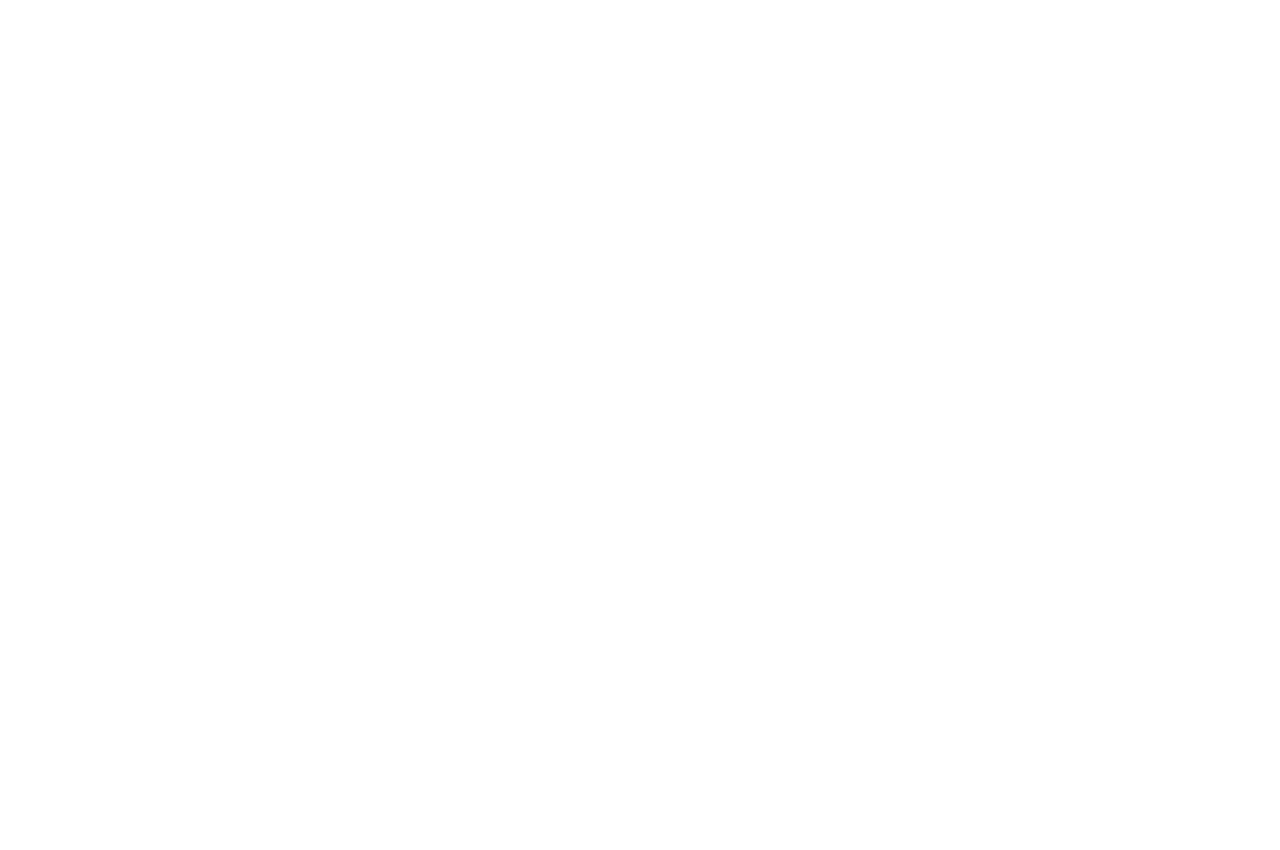
An essential part of the successful development of the plant, which is set to expand to more than 100 GWh capacity, was the careful management of the ramp-up process. The challenge was to grow while supplying quality products at the same time. Another challenge was reconciling the Korean business with the work practices and demands of OEMs such as Volkswagen. LG Chem is relatively new to the automotive industry, and language and cultural differences also added to the complexity. “Good communication is essential when operating in such dynamic conditions. Customer symposiums and R&D networks help us understand customer requirements and align our product portfolio accordingly,” says Jeong. The approach has been fruitful. “The successful introduction of the long cell technology for the revolutionary Volkswagen modular electric drive matrix is an excellent example of how our co-working with OEMs produces world-first technologies,” he says.
We want to create the green factory of the future.
Sustainability and innovation
But complexity is not the only issue the business is concerned with. Sustainability in all its multiple facets is a top priority backed by senior management at the LG Chem Group level. “Besides delivering batteries for fuel-free vehicles, we want to move on and also create the green factory of the future,” says Jeong. As OEMs seek to reduce the carbon footprint in their supply chains, more and more suppliers are switching to renewable resources. “The second priority is to maintain and further develop our competitive technology edge.” The company is investing in in-house R&D and forging partnerships with advanced battery technology companies.
The coronavirus crisis changes everything
The Covid-19 outbreak impacted the business in several ways. Internal teams had to manage the new health situation on site. Regular hand sanitation, keeping distance, and wearing masks were introduced, but these measures did not hinder operations. “Our employees reacted really well and followed the new regulations,” says Jeong. However, supplies of vital production materials were delayed due to logistical problems and shutdowns of supplier factories. LG Chem coped well with the situation thanks to sufficient stocks of raw materials, their extensive experience in managing suppliers and strong networks, and—last but not least—hard work and creativity.
A more challenging task was the ramp-up process of the production lines as the coronavirus crisis hit the industry. Interrupting the setup and training of people was simply not an option. Originally, the lines were set up and tested in South Korea and then shipped to Poland for installation. With the lockdown in place, experienced experts from South Korea were not readily available. Staff who were still in Poland extended their stay and digital remote tools assisted in the process.
Government incentives spark up markets
With consumers in lockdown and little overall commercial activity, demand from OEMs naturally shrank. “Frankly, I was wondering how to manage battery production in case we experienced a dramatic drop in demand, especially in the European market,” says Jeong. Luckily, his worries were allayed. Initiatives by European countries including Germany provided additional incentives for electric vehicles in order to help reopen the market. After a pause, OEMs slowly began production again. But as LG Chem continued manufacturing throughout the corona crisis, a proportion of the batteries produced were stockpiled by OEMs.
Battery demand worldwide
Strong growth forecast
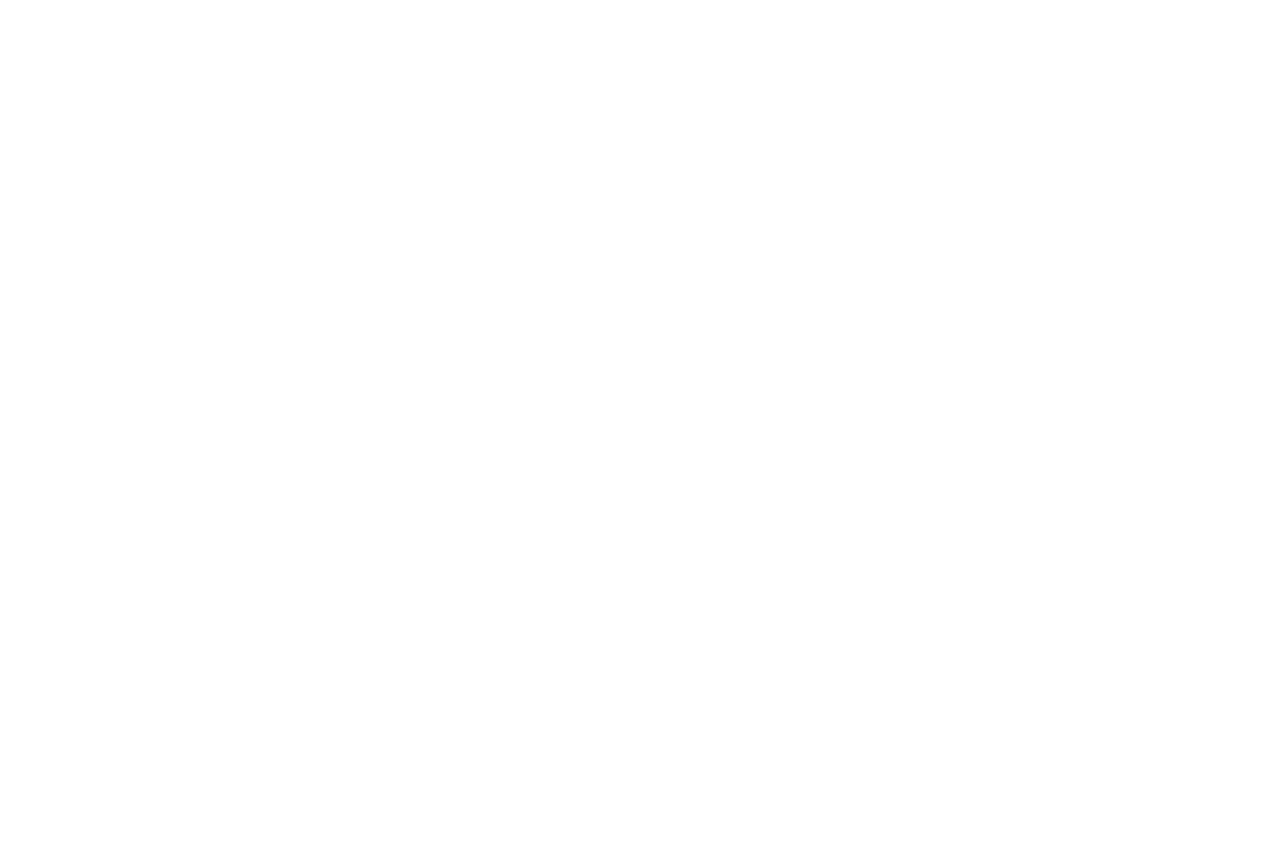
Since January 2020, LG Chem has ranked No. 1 in the European electric vehicle battery market with an 80 percent market share, according to Jeong. And globally as well, LG Chem leads the field with a market share of 24 percent (January–May 2020). It has taken significant investment to reach this position. Over the medium term, the business is focused on profitability and aims to maintain its position as market leader built on strong customer relationships. “Without a doubt, electric vehicle technology will replace the majority of combustion engines in the mid- to long term,” says Jeong. “This presents us with a great opportunity to serve the European market and engage in new developments such as the cobalt-free and solid-state batteries, which will enhance safety and performance.”